Benchtop Lab Unit
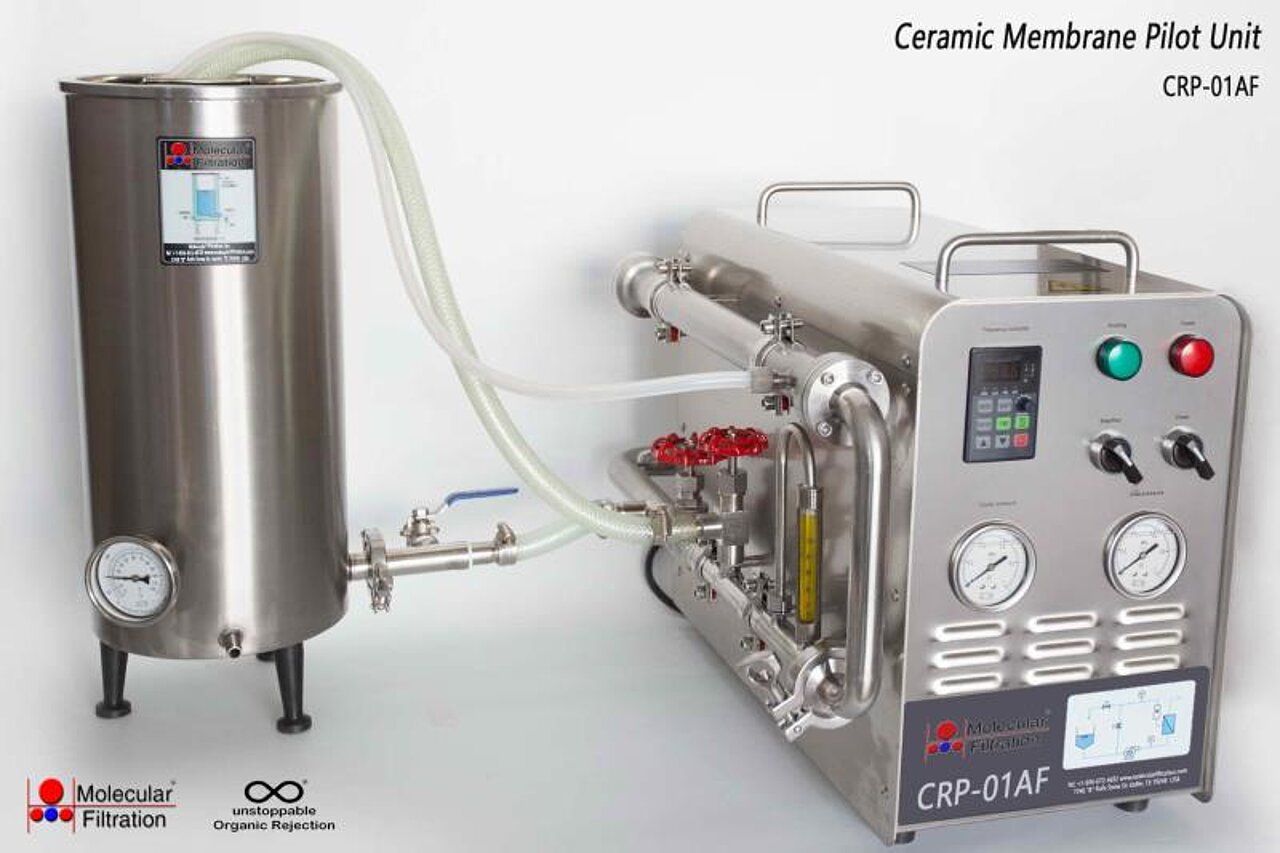
Product Overview
MFI Ceramic Membrane Table Top Pilot Unit can be used for cross flow membrane demonstration and liquid testing in small volume.
Universities, Research Institutes, Chemical, Petro-chemical, Pharmaceuticals, Biotechnology and other companies can use it as a useful tool to investigate and evaluate
membrane filtration process.
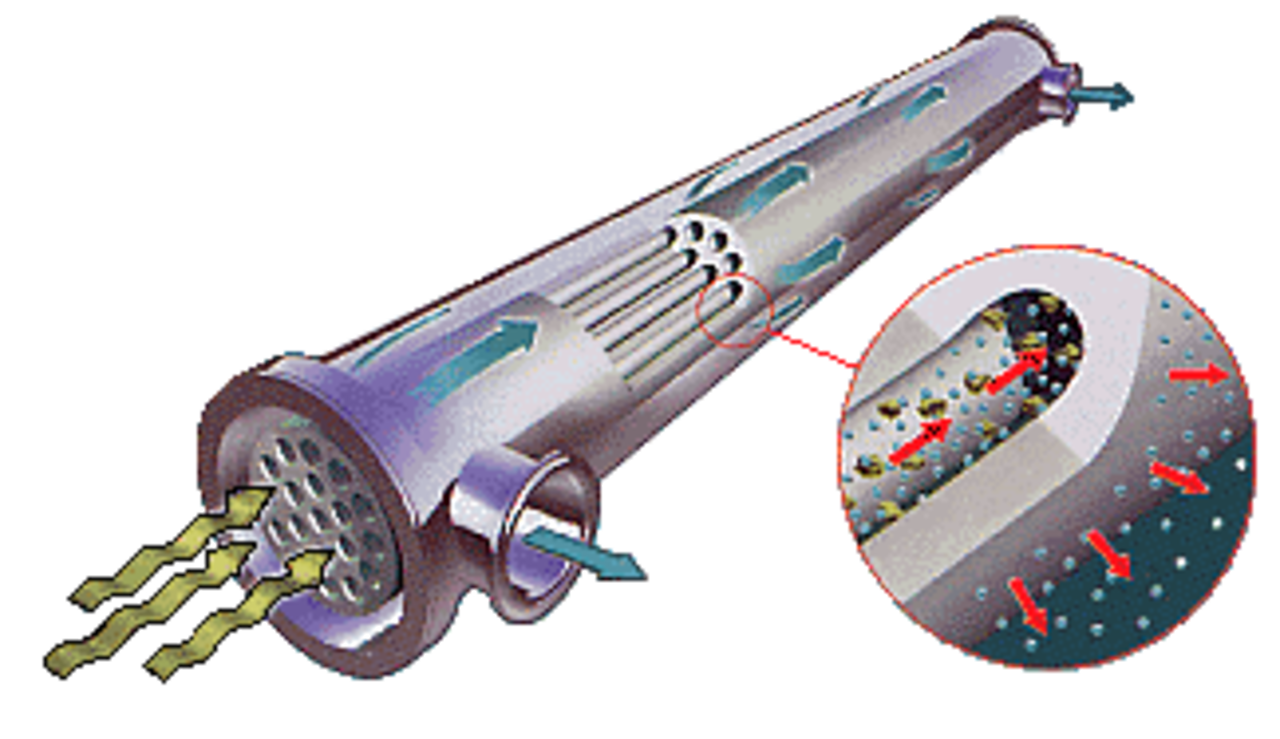
Membrane Testing - Different Configurations
Our Benchtop Lab Unit is engineered to provide unmatched versatility for membrane testing. This feature allows researchers and engineers to evaluate a wide range of membrane configurations, ensuring optimal performance for specific applications. Key capabilities include:
- Channel Diameter Testing:
Test membranes with varying channel diameters to determine the most efficient flow dynamics for your process. The unit accommodates multiple channel sizes, making it adaptable for diverse operational needs. - Porosity Variations:
Evaluate membranes with different pore sizes to identify the best option for your filtration objectives. Whether your goal is precise particle separation, oil removal, or other specialized filtration, this unit ensures you can find the ideal porosity. - Array of Membrane Configurations:
From flat sheets to tubular and spiral wound membranes, the Benchtop Lab Unit supports a comprehensive array of configurations. This flexibility allows users to simulate industrial processes and scale up with confidence.
Why This Matters
By enabling comprehensive membrane testing, the Benchtop Lab Unit minimizes guesswork and accelerates decision-making for process optimization. Whether you're conducting research or validating a new design, this feature empowers you to achieve precision and efficiency.
Process Flow Description:
- Feed Solution Input:
- The solution starts in the feed tank and is drawn by the pump.
- Circulation Through the Filtration Unit:
- The pump pushes the solution through the filtration unit, where membranes filter the liquid.
- Separation into Permeate and Retentate:
- Permeate exits as the clean, filtered liquid.
- Retentate can either be discharged or sent back to the feed tank for further processing.
- Monitoring and Control:
- The pressure gauges help maintain optimal operating conditions, preventing damage to the membranes.
Technical Specifications
Machine Name: | Table Top Pilot Unit |
Model: | CRP-01AF |
Process Control: | Optimize - VFD control |
Desktop Size: | 54 x 35 x 47 cm. |
Membrane Model: | MFM30-19 |
Number of Channel: | 19 channels |
Membrane Diameter: | 30 mm |
Membrane Length: | 500 mm |
Membrane Pore sizes: | 30, 50, 100, 200, 500 nm |
Operating Pressure: | 30, 50, 100, 200, 500 nm |
Holding Tank Volume: | 2.0 L - Jacket Tank |
Material of Construction: | Sanitary SS316 |
Gross Weight: | 35 Kg. |
Applications
1. Research and Development (R&D)
- Evaluating and optimizing membrane performance for new filtration processes.
- Testing various membrane types, pore sizes, and channel configurations.
- Developing scalable filtration solutions for industrial applications.
2. Process Validation
- Simulating real-world filtration processes on a small scale.
- Validating membrane compatibility with specific feed solutions.
- Assessing separation efficiency and membrane durability under different conditions.
3. Water Treatment
- Testing membranes for removing impurities, suspended solids, and contaminants.
- Evaluating processes for desalination, demineralization, and water reuse.
- Researching effective methods for oil and grease removal in produced water.
4. Food and Beverage Industry
- Concentrating and clarifying juices, milk, and other liquid products.
- Testing for separation of proteins, sugars, and other valuable components.
- Optimizing filtration for microbial removal to ensure product safety.
5. Pharmaceutical and Biotech Applications
- Separating and concentrating bioactive compounds.
- Testing molecularfiltration, ultrafiltration and microfiltration processes for drug development.
- Assessing membrane performance for sterile filtration.
6. Chemical and Petrochemical Industry
- Testing membranes for separating oil-water emulsions.
- Researching filtration processes for chemical recovery and purification.
- Validating solutions for wastewater treatment and reuse.
7. Academic and Educational Use
- Training students and researchers on membrane technology and filtration principles.
- Demonstrating cross-flow filtration processes in a controlled environment.